Dual 721 Service Manual 2
This is the 25 pages manual for Dual 721 Service Manual 2.
Read or download the pdf for free. If you want to contribute, please upload pdfs to audioservicemanuals.wetransfer.com.
Page: 1 / 25
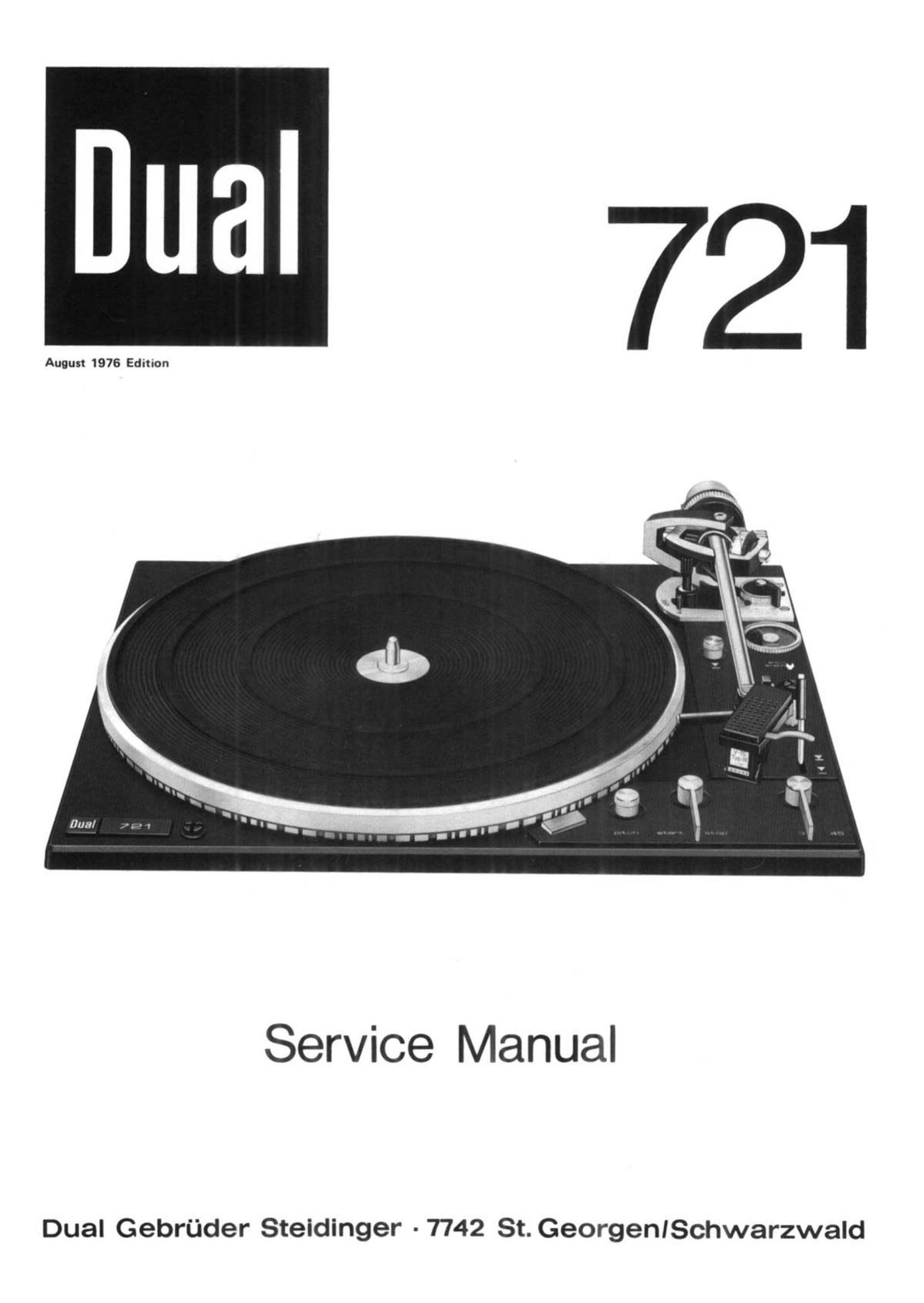