Panasonic se fx 60 te service manual
This is the 64 pages manual for panasonic se fx 60 te service manual.
Read or download the pdf for free. If you want to contribute, please upload pdfs to audioservicemanuals.wetransfer.com.
Page: 1 / 64
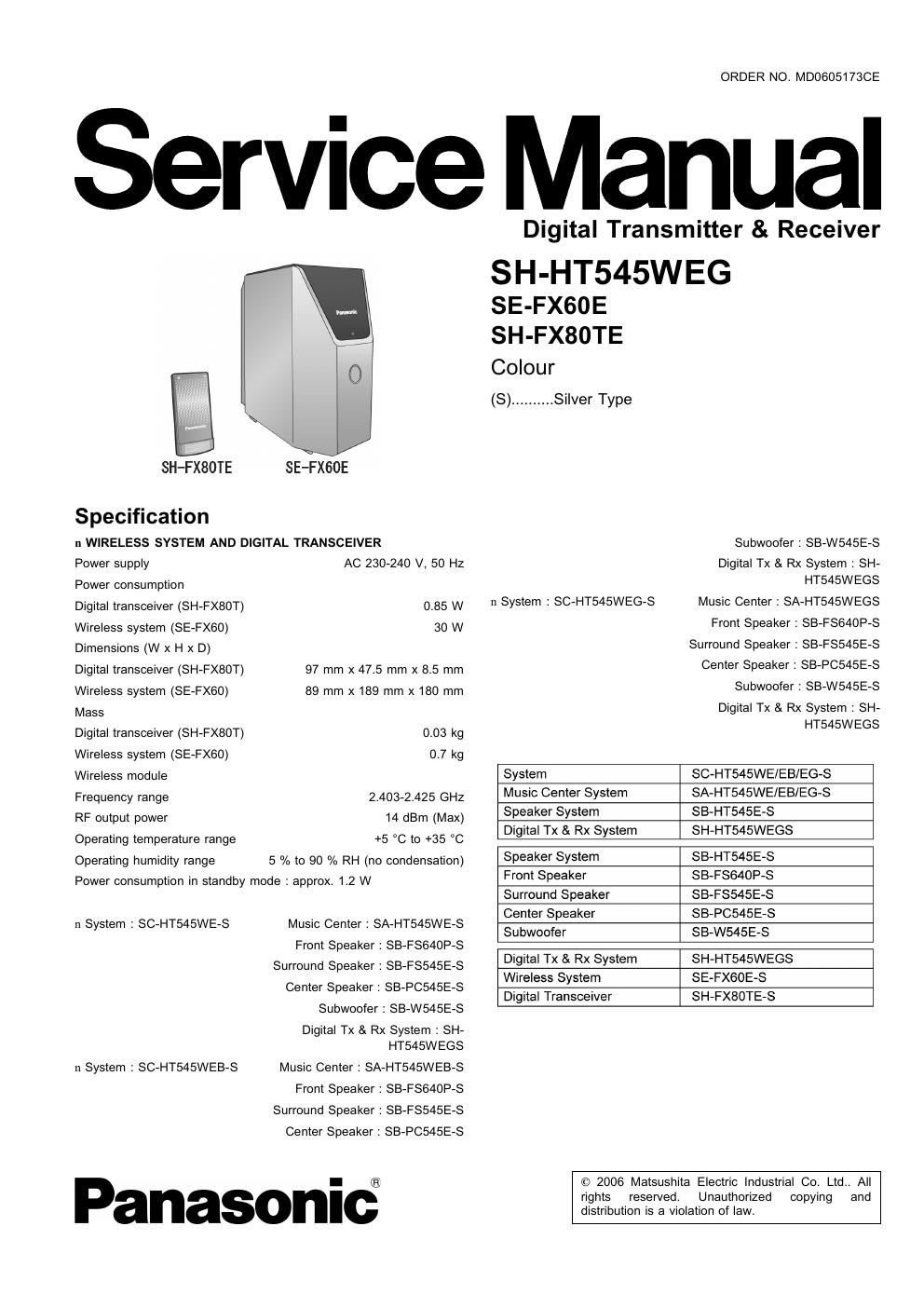