Nad T 517 C Service Manual
This is the 78 pages manual for Nad T 517 C Service Manual.
Read or download the pdf for free. If you want to contribute, please upload pdfs to audioservicemanuals.wetransfer.com.
Page: 1 / 78
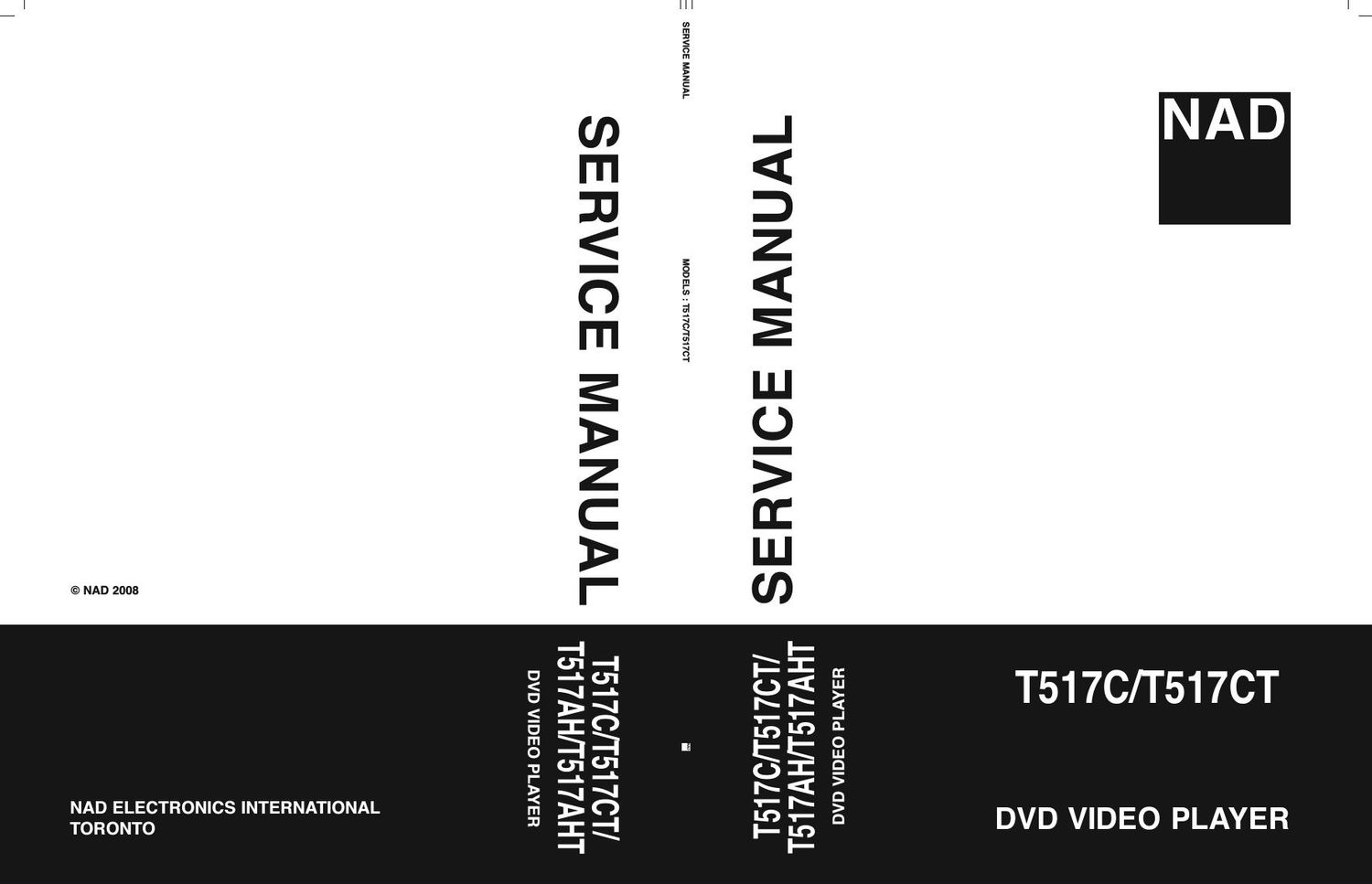