Kenwood AT 300 Service Manual
This is the 23 pages manual for Kenwood AT 300 Service Manual.
Read or download the pdf for free. If you want to contribute, please upload pdfs to audioservicemanuals.wetransfer.com.
Page: 1 / 23
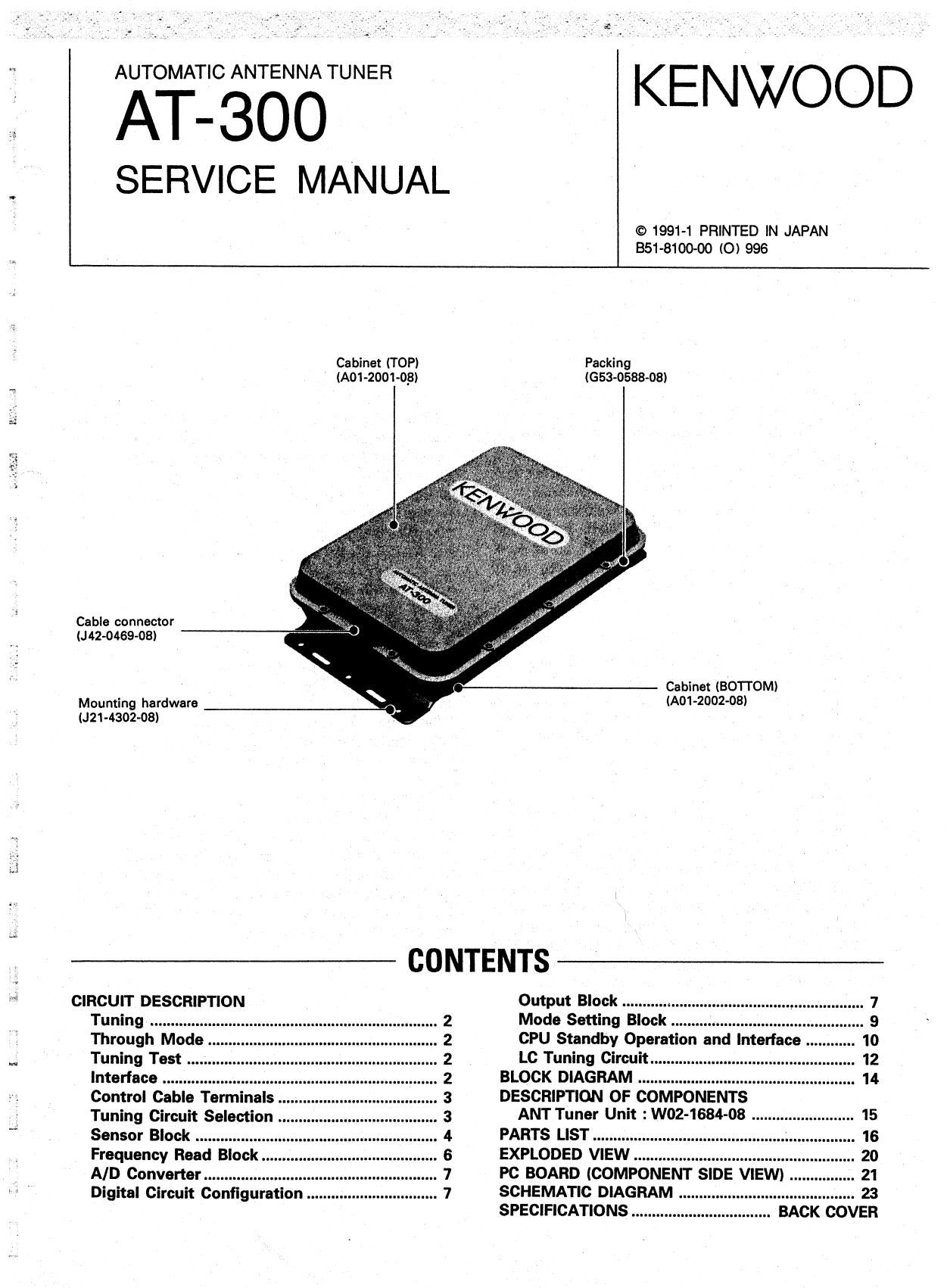