Jvc XVS 56 BK Service Manual
This is the 72 pages manual for Jvc XVS 56 BK Service Manual.
Read or download the pdf for free. If you want to contribute, please upload pdfs to audioservicemanuals.wetransfer.com.
Page: 1 / 72
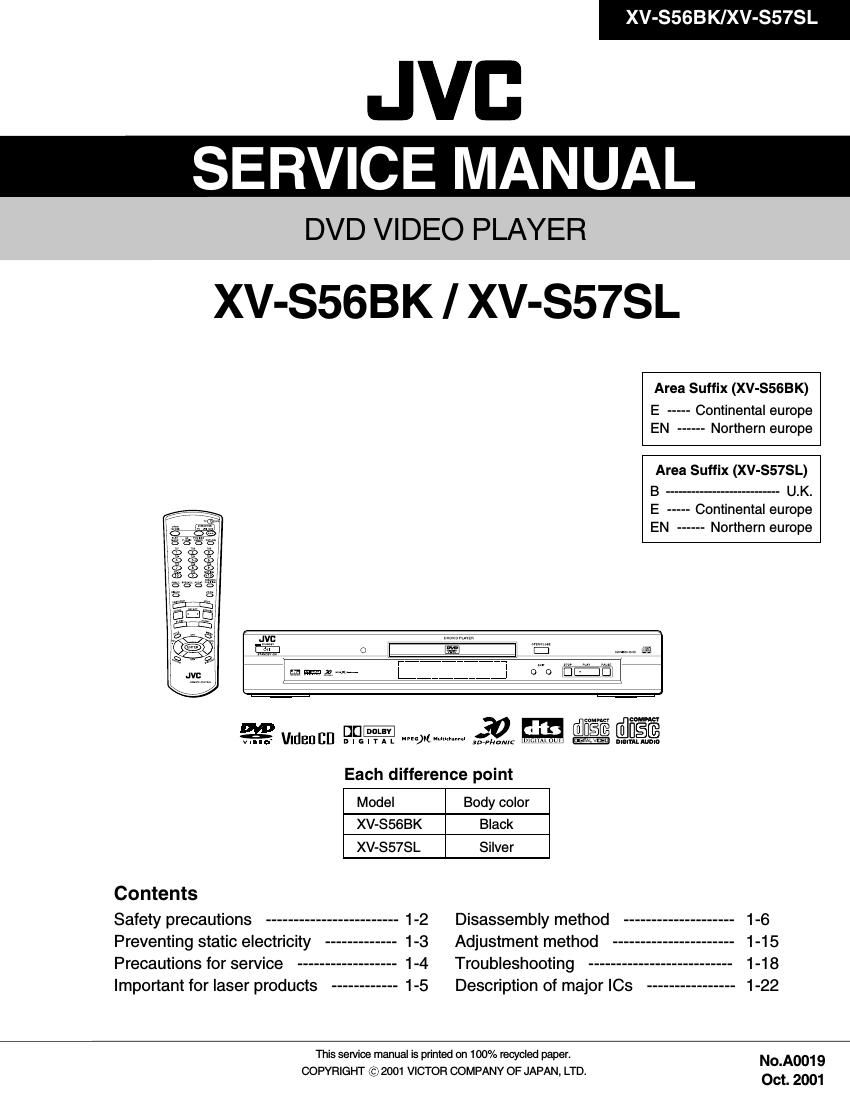