Jvc UXF 70 MD Service Manual
This is the 112 pages manual for Jvc UXF 70 MD Service Manual.
Read or download the pdf for free. If you want to contribute, please upload pdfs to audioservicemanuals.wetransfer.com.
Page: 1 / 112
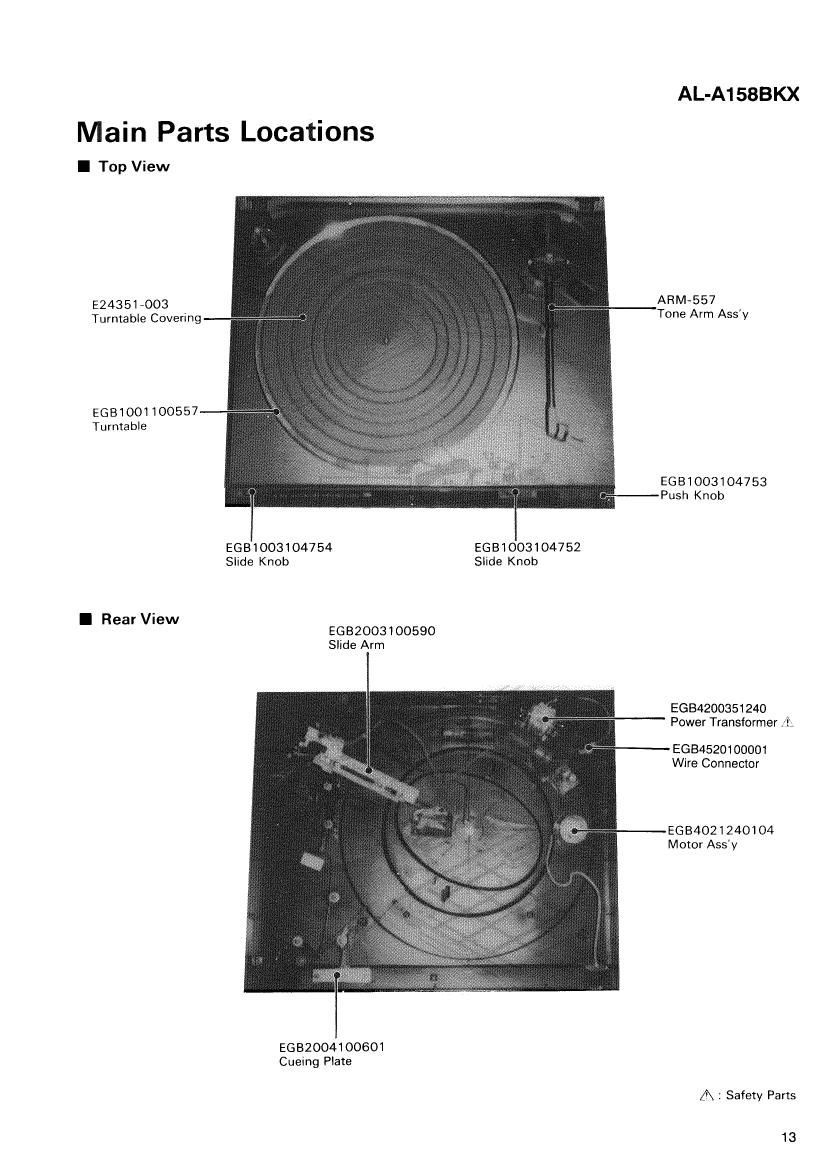