Jvc UX 1000 GR Service Manual
This is the 80 pages manual for Jvc UX 1000 GR Service Manual.
Read or download the pdf for free. If you want to contribute, please upload pdfs to audioservicemanuals.wetransfer.com.
Page: 1 / 80
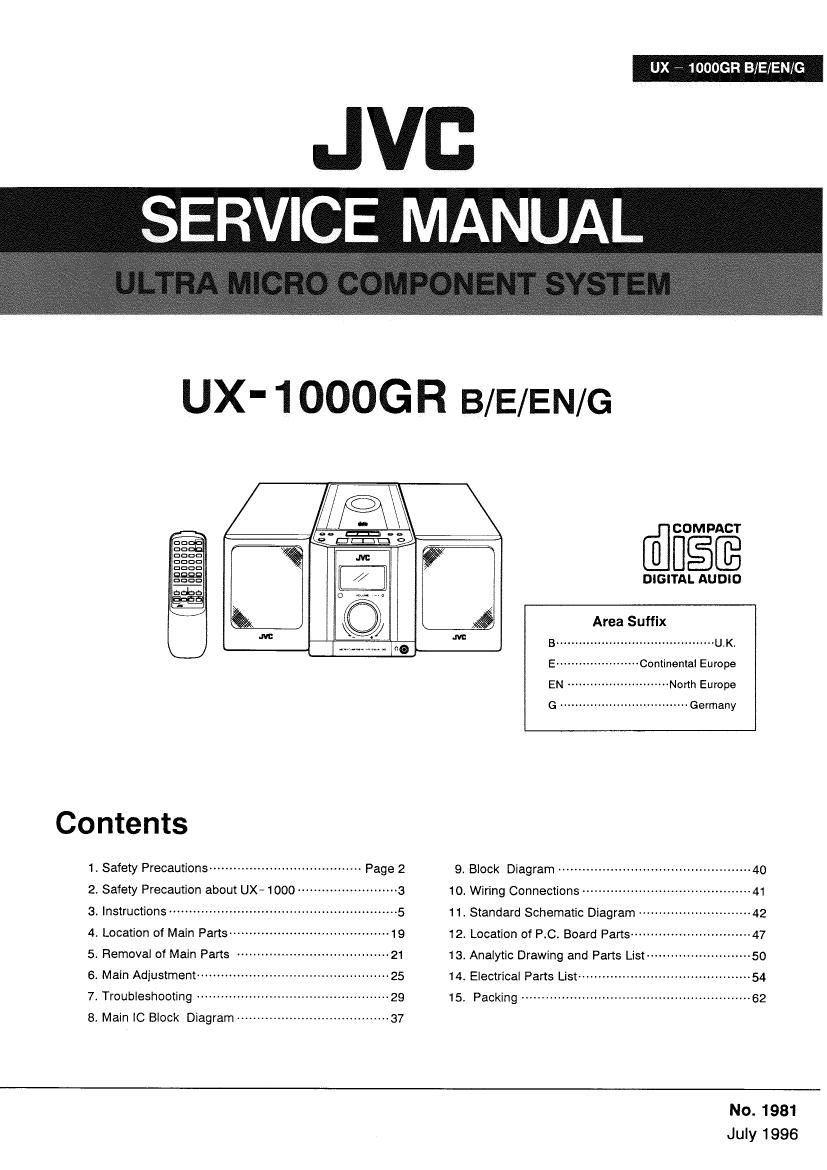