Heathkit HW 5400 Manual
This is the 263 pages manual for Heathkit HW 5400 Manual.
Read or download the pdf for free. If you want to contribute, please upload pdfs to audioservicemanuals.wetransfer.com.
Page: 1 / 263
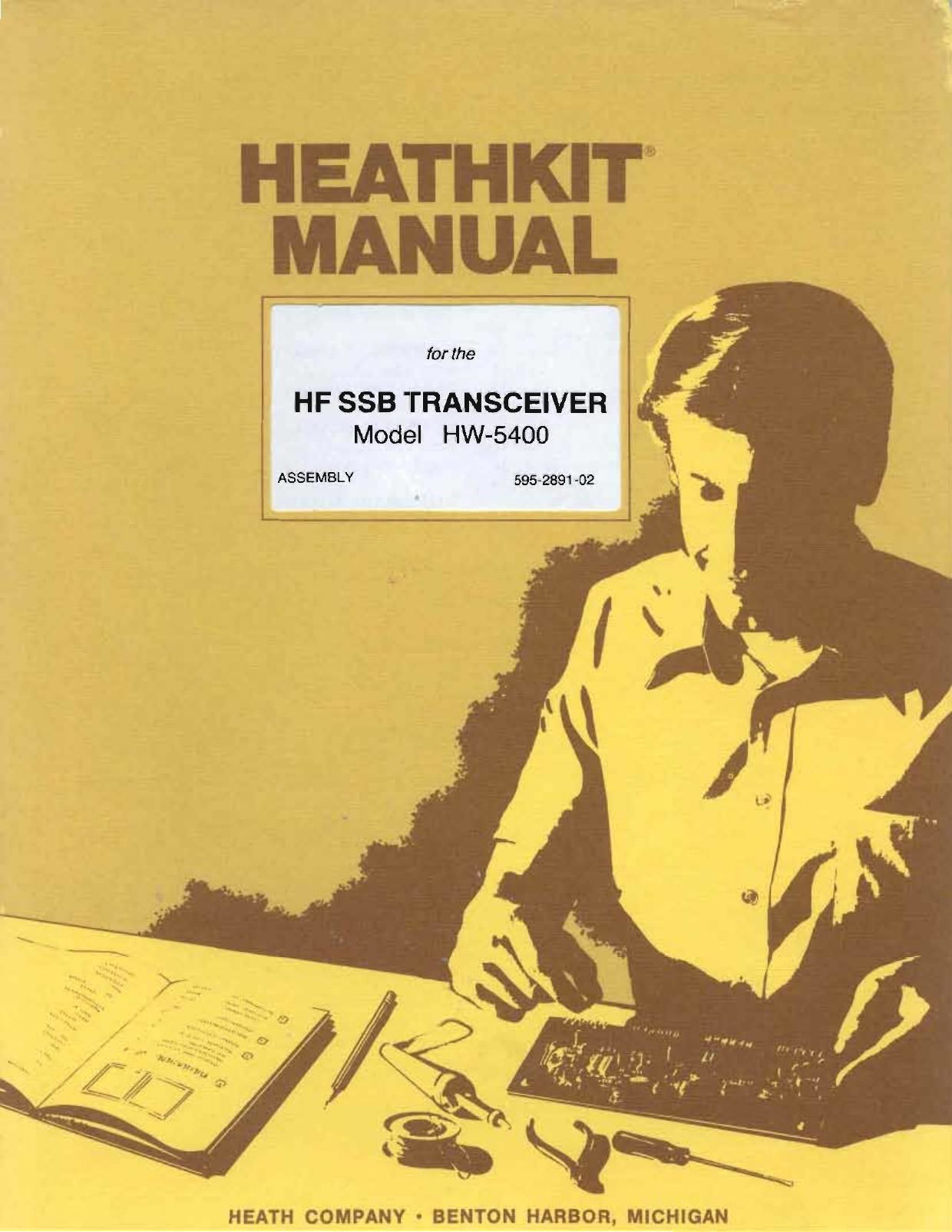