Fisher 504 Service Manual
This is the 24 pages manual for Fisher 504 Service Manual.
Read or download the pdf for free. If you want to contribute, please upload pdfs to audioservicemanuals.wetransfer.com.
Page: 1 / 24
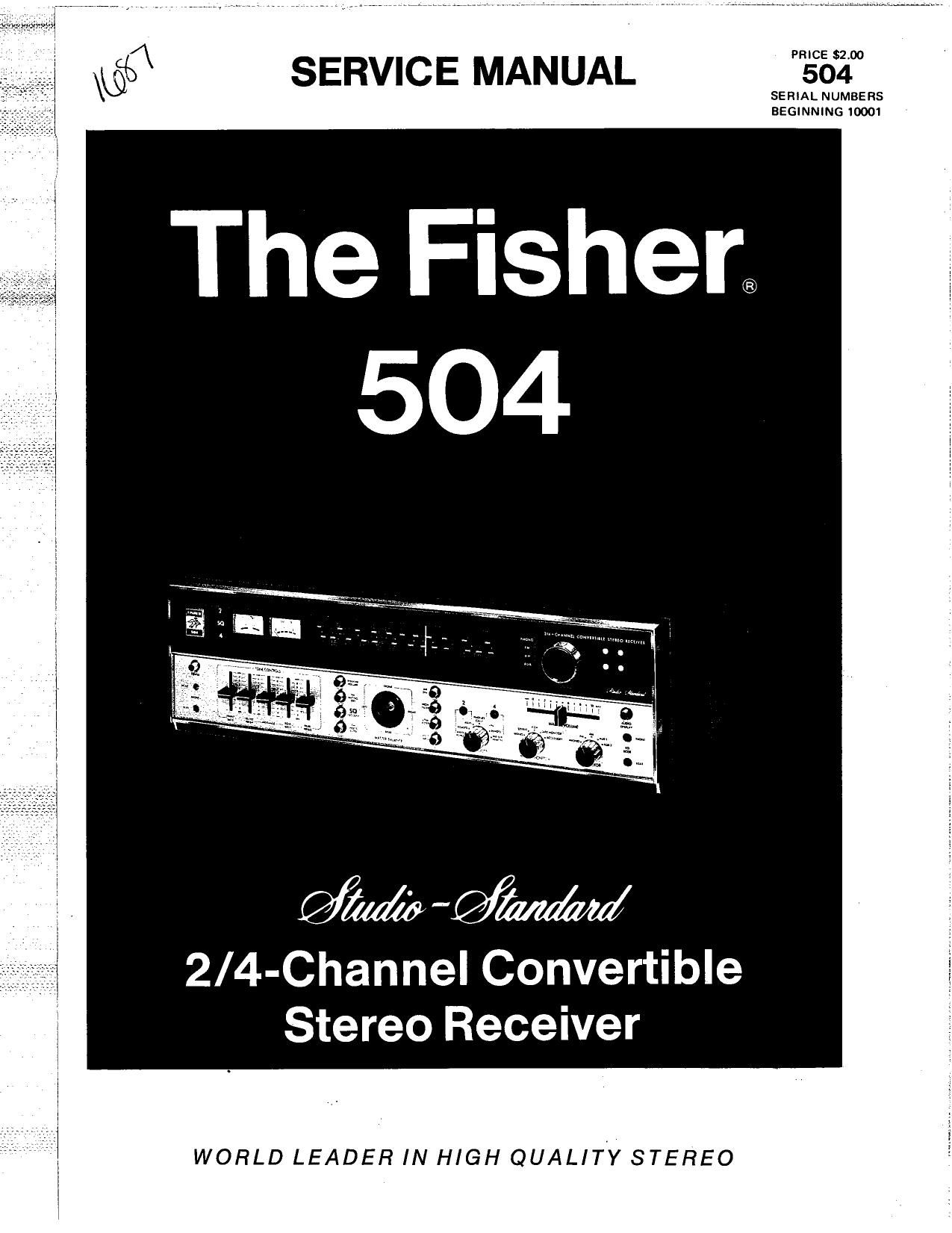