Fisher 180 Service Manual
This is the 12 pages manual for Fisher 180 Service Manual.
Read or download the pdf for free. If you want to contribute, please upload pdfs to audioservicemanuals.wetransfer.com.
Page: 1 / 12
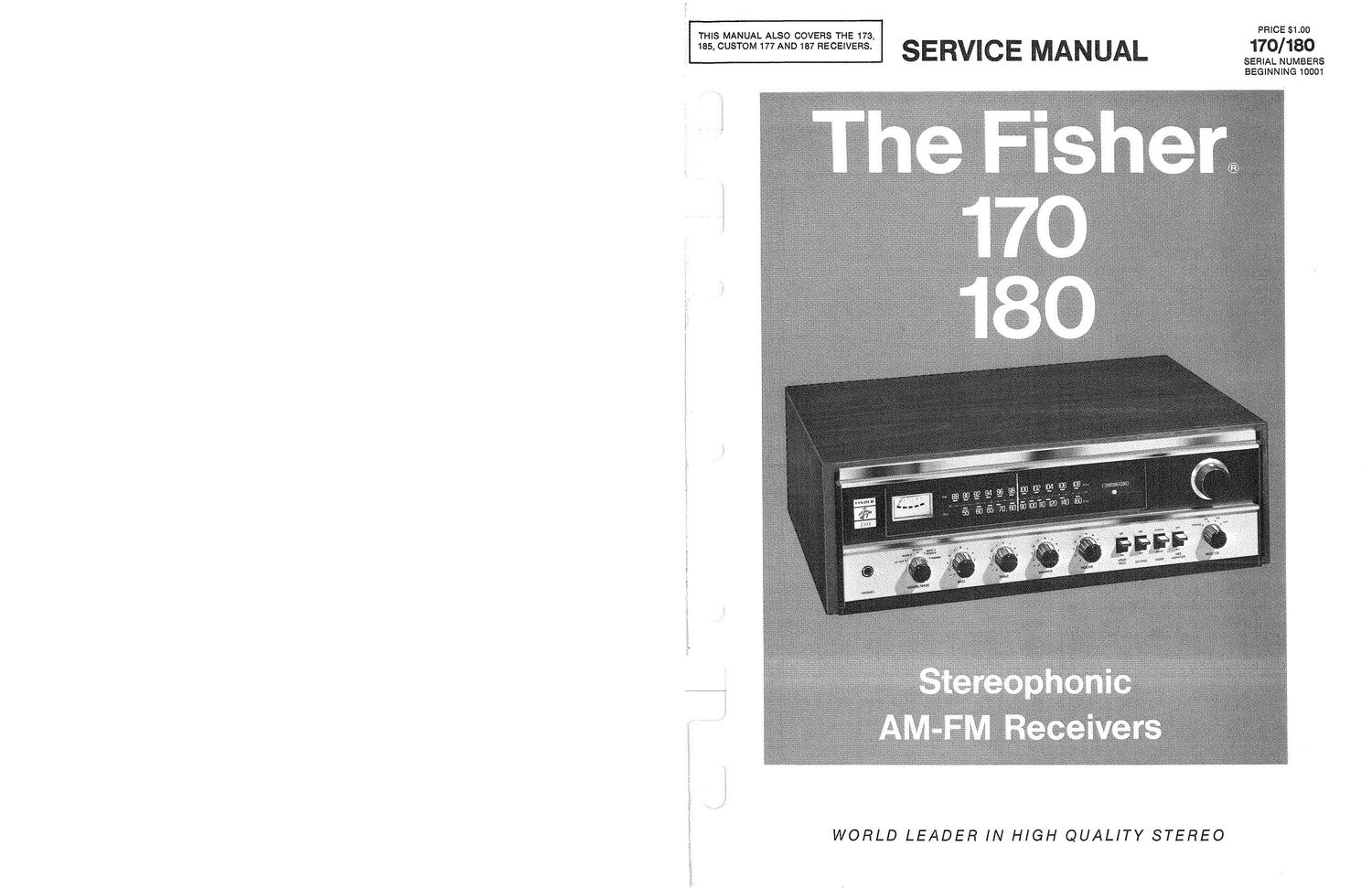