Dynaco ST 120 Owners Manual
This is the 26 pages manual for Dynaco ST 120 Owners Manual.
Read or download the pdf for free. If you want to contribute, please upload pdfs to audioservicemanuals.wetransfer.com.
Page: 1 / 26
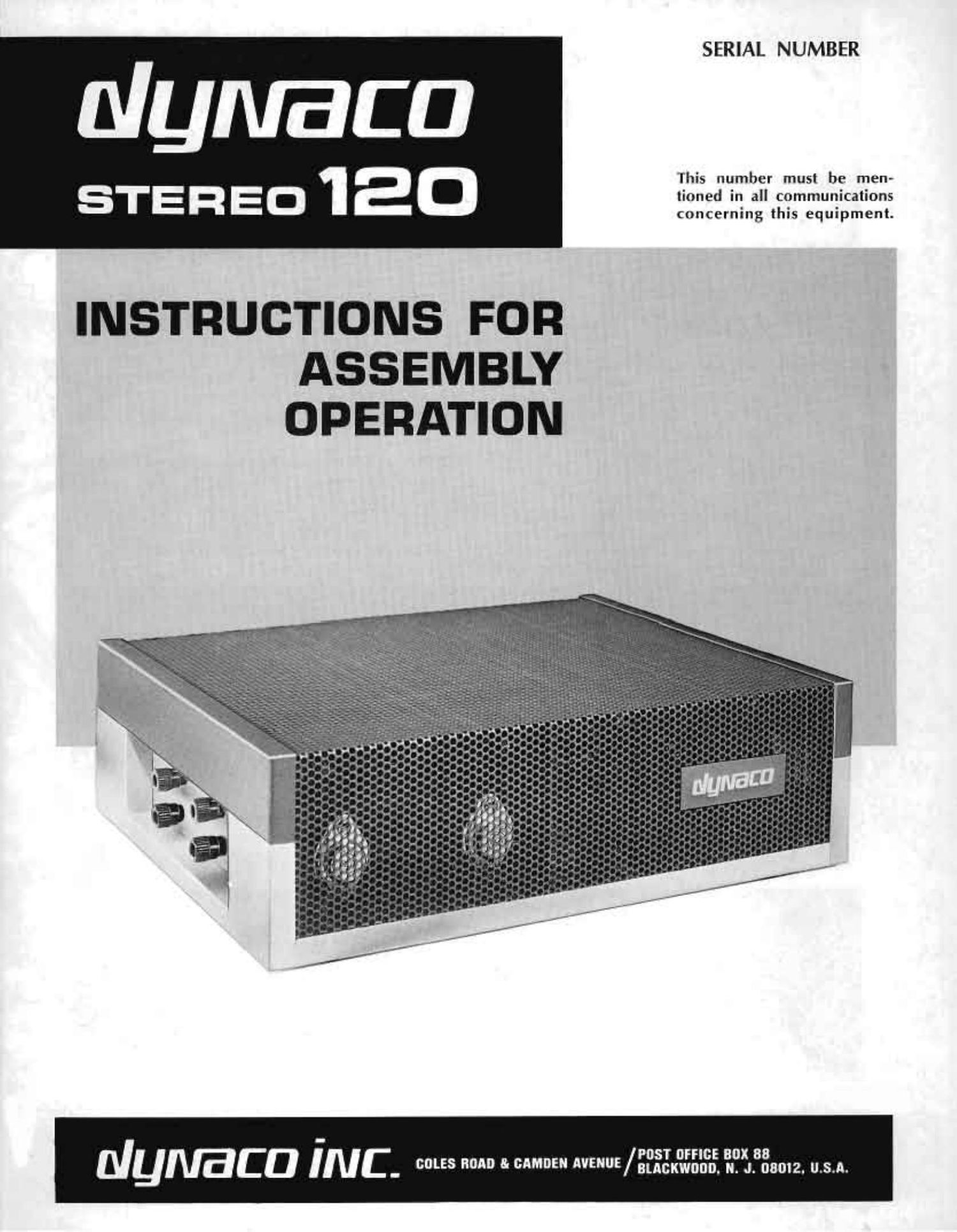