Dynaco Dynakit ST 70 Owners Manual
This is the 18 pages manual for Dynaco Dynakit ST 70 Owners Manual.
Read or download the pdf for free. If you want to contribute, please upload pdfs to audioservicemanuals.wetransfer.com.
Page: 1 / 18
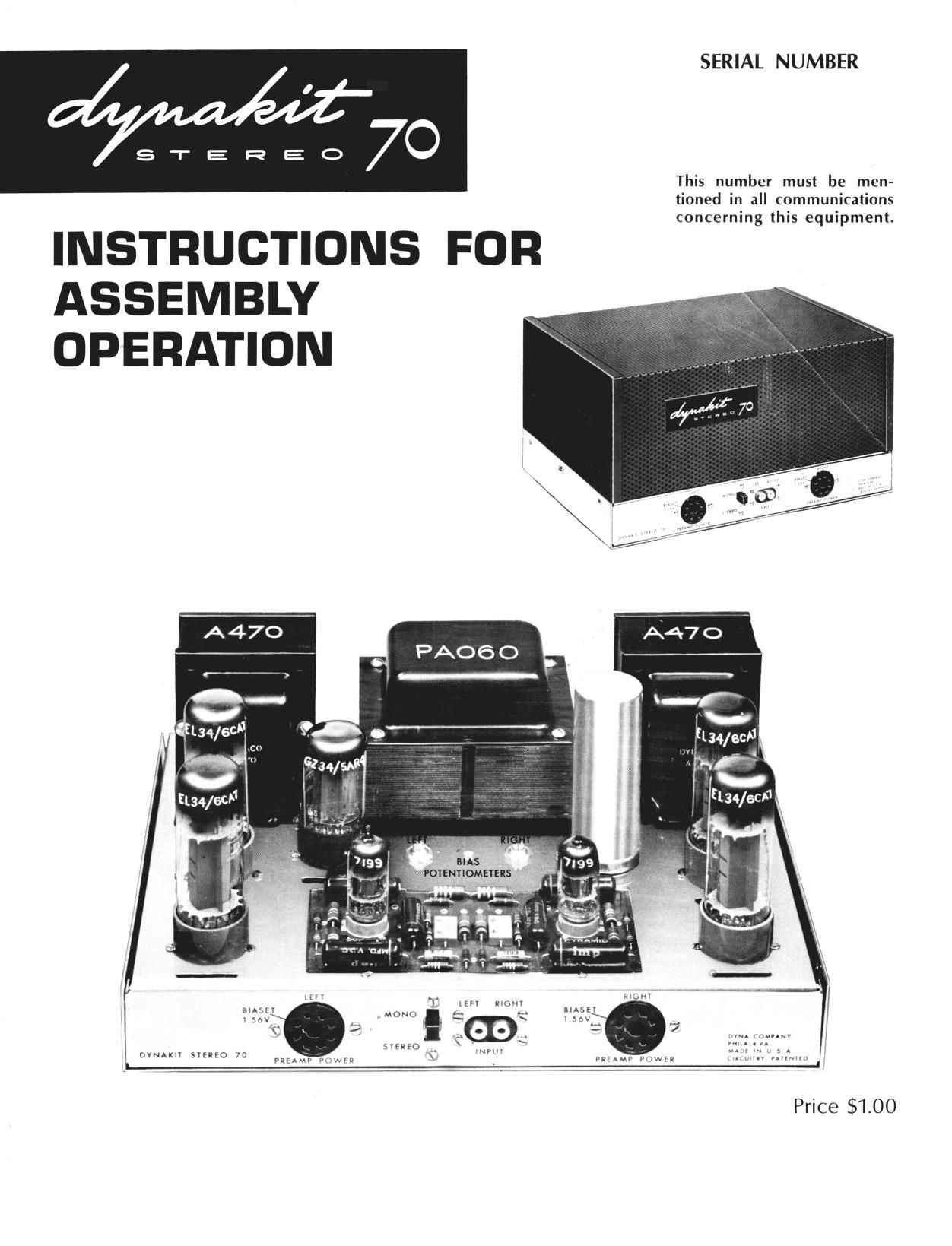