Dynaco Dynakit DSC 1 Service Manual
This is the 10 pages manual for Dynaco Dynakit DSC 1 Service Manual.
Read or download the pdf for free. If you want to contribute, please upload pdfs to audioservicemanuals.wetransfer.com.
Page: 1 / 10
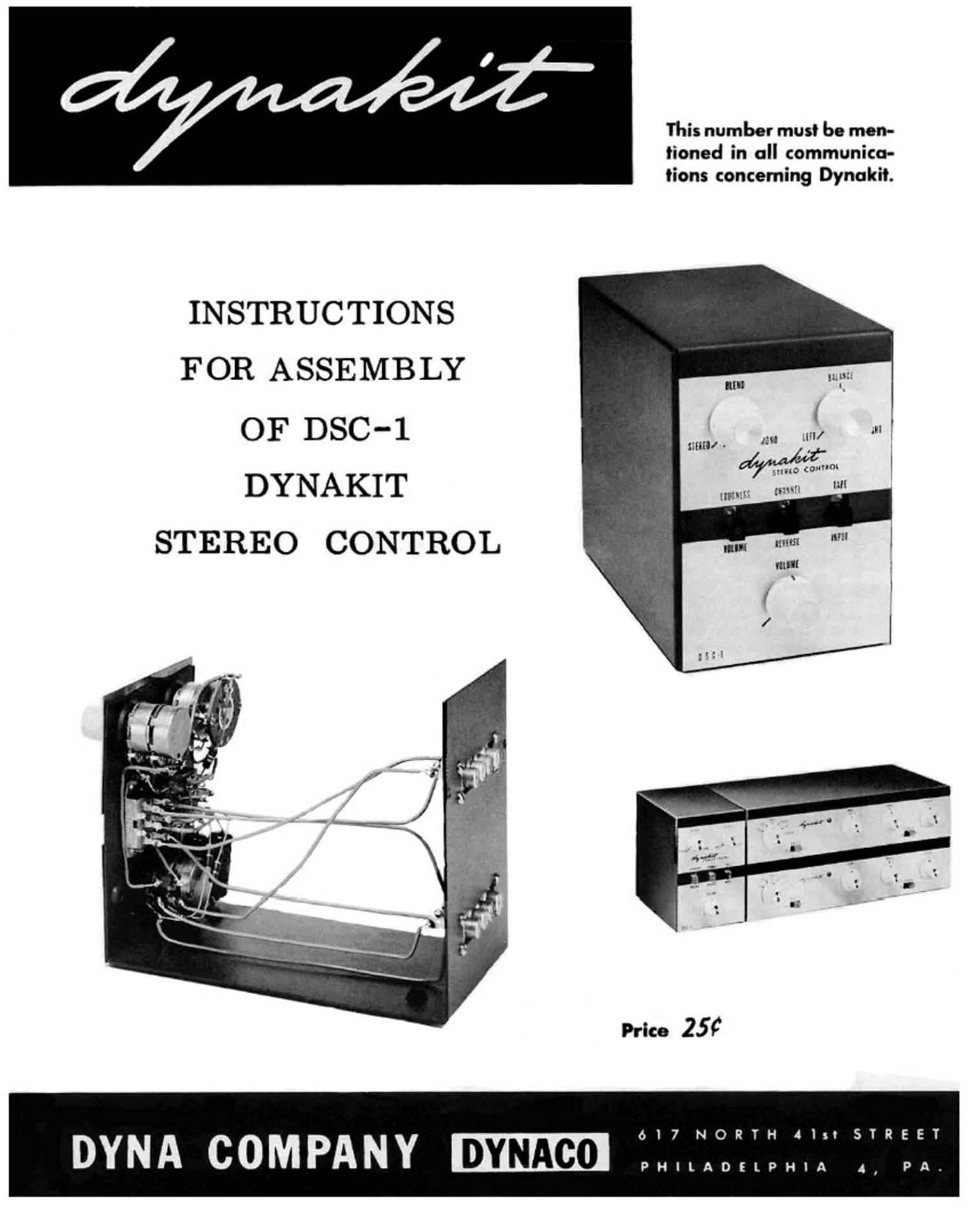