Akai AC 10 Service Manual
This is the 63 pages manual for Akai AC 10 Service Manual.
Read or download the pdf for free. If you want to contribute, please upload pdfs to audioservicemanuals.wetransfer.com.
Page: 1 / 63
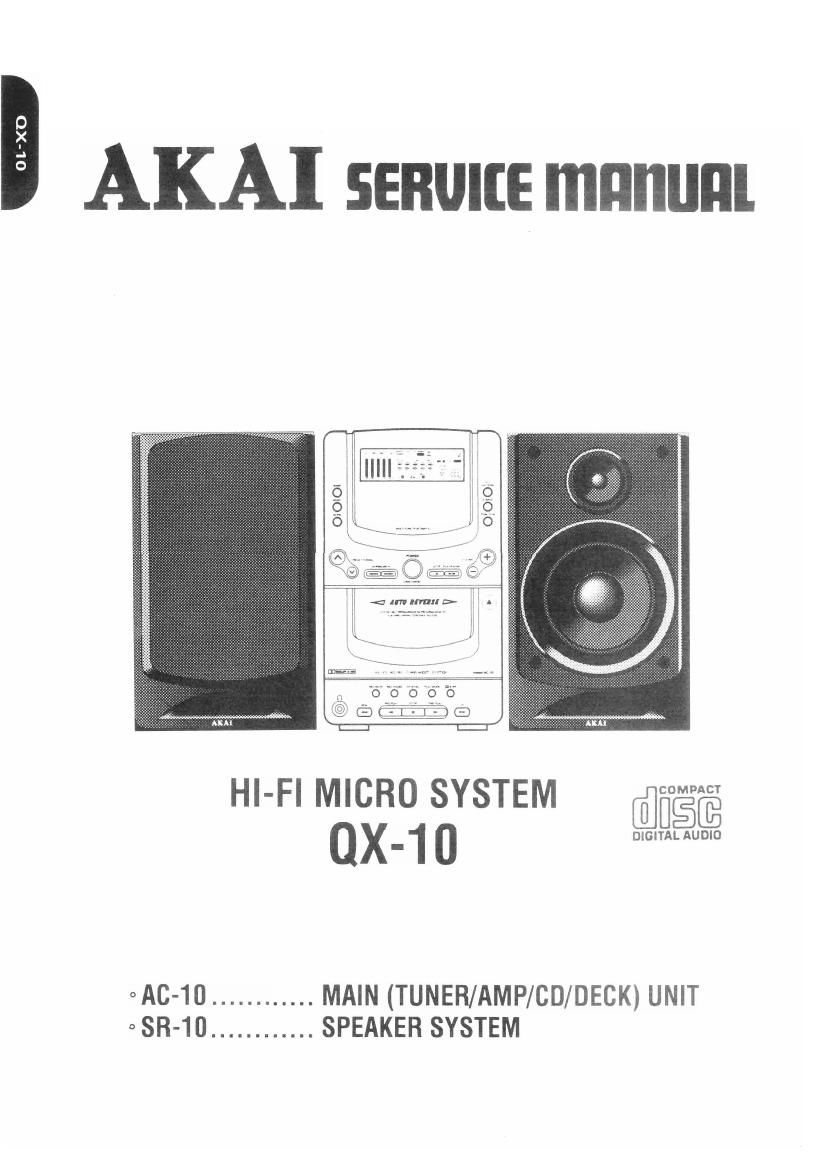